Soldering is one of the most essential steps in Printed Circuit Board assembly, ensuring that electronic components are securely and electrically connected to the board. The type of solder used, lead solder or lead-free solder—has a direct impact on product reliability, manufacturing cost, environmental safety, and compliance with international regulations.
In this article, we'll explore what lead and lead-free solder are, how they differ, their respective advantages and disadvantages, their environmental impact, and other important knowledge for PCB manufacturing and design.
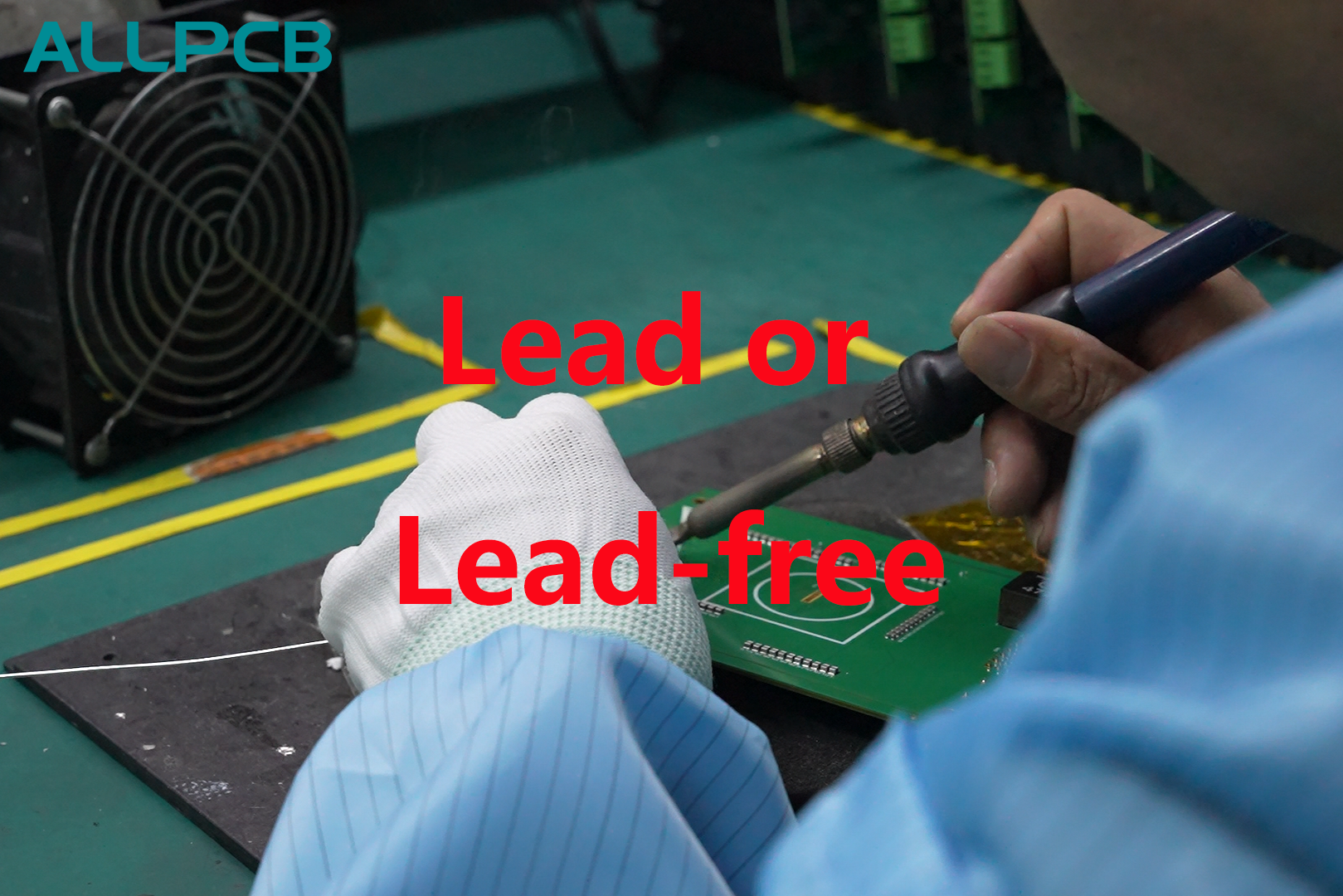
What is Lead Solder?
Lead solder is a traditional solder alloy primarily composed of tin (Sn) and lead (Pb). The most commonly used formulation is Sn63/Pb37 (63% tin and 37% lead), which is a eutectic alloy—meaning it has a single melting point (183°C) and changes from solid to liquid instantly, providing a smooth and efficient soldering process.
Lead solder has been widely used for decades due to its excellent wetting ability, low melting temperature, and ease of rework.
What is Lead-Free Solder?
Lead-free solder refers to solder alloys that do not contain lead, often composed of tin, combined with metals like silver (Ag), copper (Cu), bismuth (Bi), or antimony (Sb). One of the most common types is SAC305, which contains 96.5% tin, 3.0% silver, and 0.5% copper.
Lead-free solder was developed in response to global environmental regulations, especially the RoHS directive from the European Union, which bans the use of lead in most electronic products.
Key Differences Between Lead and Lead-Free Solder
Advantages and Disadvantages of Lead Solder
Advantages
- Lower melting point, reducing the thermal stress on components.
- Superior wetting properties ensure reliable joints.
- Easier for manual soldering and rework.
- Smooth and shiny solder joints are easier to inspect visually.
- Cost-effective and widely available.
Disadvantages
- Toxicity: Lead is harmful to human health and the environment.
- Regulatory Restrictions: Not allowed in most consumer products due to RoHS and other regulations.
- Disposal and recycling of lead-containing electronics are more complex.
Advantages and Disadvantages of Lead-Free Solder
Advantages
- Environmentally friendly and RoHS compliant.
- Safer for workers and end users.
- Better suited for high-temperature applications (e.g., automotive, industrial).
- Compatible with modern manufacturing processes.
Disadvantages
- Requires higher processing temperatures, which can damage sensitive components.
- Solder joints are often more brittle and less shiny.
- More expensive due to the use of silver or specialty metals.
- Slightly harder to rework and inspect.
Environmental and Health Impact
Lead is a well-known neurotoxin that poses serious health risks, especially with prolonged exposure. In manufacturing environments, solder fumes or dust containing lead can be dangerous. Improper disposal of electronics with lead solder can also contaminate soil and groundwater.
Lead-free solder was introduced to reduce toxic waste, improve worker safety, and protect ecosystems. Regulations like RoHS, WEEE, and China RoHS have significantly driven the global shift toward lead-free manufacturing.
Additional Considerations and Tips
- Thermal Profiles: Lead-free solder requires different reflow oven settings. Make sure your PCB design and components can withstand the higher temperatures.
- Material Compatibility: Not all components are equally compatible with both types of solder. Some legacy parts may still require lead-based soldering.
- Mixed Assembly: In rare cases, mixed lead and lead-free processes are used, but this is complex and discouraged due to potential reliability issues.
- Storage and Shelf Life: Lead-free solders tend to oxidize faster; proper storage in dry, cool environments is essential.
- Inspection and Testing: Automated Optical Inspection (AOI) systems may need tuning due to the dull appearance of lead-free joints.
Which Solder is Better: Lead or Lead-Free Solder?
Leaded solder is easier to use, has a lower melting point, is low cost, and causes fewer quality problems with the solder joints than lead-free solder, however; the continued efforts to take lead out of all electronic products in the United States means that leaded solder could be obsolete in the next 10 years in numerous commercial applications.
Generally, it is more economical and effective to use lead solder because of its unique properties and benefits. There continue to be some industries that use leaded solders because of these properties and benefits.
The primary reason you should opt for lead-free solders, if you are able to, is if your government prohibits lead from being used in products or if you are working to be an Environmental, Social, and Corporate Governance (ESG) company.
All sectors that use solder in large quantities are likely to shift to lead-free soldering soon if they have not done so yet. The paint and gasoline sectors have both gone lead-free. As manufacturers begin to shift away from leaded solder, make sure you are up to date on your training and learn more about lead-free solder and leaded soldering from industry experts with ALLPCB.
Conclusion
Choosing between lead solder and lead-free solder is not just a technical decision—it’s also a matter of compliance, sustainability, and product lifecycle strategy. While lead solder remains popular in specific industrial applications, the future is clearly moving toward lead-free solutions driven by safety and environmental concerns.
Understanding the differences helps engineers, designers, and manufacturers make informed decisions to ensure reliability, safety, and regulatory compliance in PCB production.